Wiring Harness for Knock Sensor Chart and Diagram
A wiring harness for a knock sensor is a set of electrical wires that connect the knock sensor to the engine control unit (ECU). The knock sensor is a device that detects the presence of knocking in the engine, which can be caused by a number of factors, such as incorrect timing or a lean air-fuel mixture. The ECU uses the signal from the knock sensor to adjust the engine timing and fuel mixture to prevent knocking.
There are a number of different types of wiring harnesses for knock sensors, depending on the make and model of the vehicle. However, all wiring harnesses for knock sensors will typically include the following components:
- A connector that plugs into the knock sensor
- A connector that plugs into the ECU
- A length of wire that connects the two connectors
When creating a wiring harness for a knock sensor, it is important to use the correct type of wire and connectors. The wire should be able to withstand the high temperatures and vibrations that are present in the engine compartment. The connectors should be able to make a good electrical connection and should be protected from moisture and corrosion.
Once the wiring harness is complete, it should be tested to ensure that it is functioning properly. This can be done by using a multimeter to check the continuity of the wires and the resistance of the connectors.
Benefits of using a wiring harness for a knock sensor:
- Prevents knocking in the engine
- Improves engine performance
- Reduces emissions
- Extends the life of the engine
Conclusion:
A wiring harness for a knock sensor is an important part of the engine management system. By preventing knocking, a wiring harness for a knock sensor can help to improve engine performance, reduce emissions, and extend the life of the engine.
Wiring Harness for Knock Sensor
A wiring harness for a knock sensor is an essential part of the engine management system. It plays a crucial role in preventing knocking, improving engine performance, and reducing emissions. Here are seven key aspects of a wiring harness for a knock sensor:
- Connector: Connects the wiring harness to the knock sensor.
- Wire: Conducts electrical signals between the knock sensor and the ECU.
- Length: Determines the reach of the wiring harness.
- Resistance: Measures the opposition to electrical flow through the wire.
- Continuity: Ensures a complete electrical path through the wiring harness.
- Shielding: Protects the wiring harness from electromagnetic interference.
- Durability: Withstands the harsh conditions of the engine compartment.
These key aspects work together to ensure that the wiring harness for a knock sensor functions properly. The connector provides a secure connection between the wiring harness and the knock sensor. The wire conducts electrical signals with minimal resistance, ensuring that the ECU receives a clear signal from the knock sensor. The length of the wiring harness allows for proper placement of the knock sensor in the engine compartment. The shielding protects the wiring harness from electromagnetic interference, which can disrupt the electrical signals. The durability of the wiring harness ensures that it can withstand the high temperatures and vibrations present in the engine compartment.
Overall, these key aspects of a wiring harness for a knock sensor are essential for ensuring that the knock sensor can effectively detect knocking in the engine and send a signal to the ECU. By understanding these key aspects, technicians can better diagnose and repair problems with the wiring harness for a knock sensor, ensuring that the engine management system is functioning properly.
Connector
The connector is a crucial component of the wiring harness for a knock sensor. It provides a secure and reliable connection between the wiring harness and the knock sensor, ensuring that electrical signals can be transmitted effectively.
-
Facet 1: Types of Connectors
Connectors for wiring harnesses come in various types, each designed for specific applications. In the case of knock sensors, common connector types include Deutsch connectors, Metri-Pack connectors, and Weather-Pack connectors. These connectors are known for their durability, resistance to moisture and corrosion, and ability to withstand the harsh conditions of the engine compartment. -
Facet 2: Pin Configuration
The pin configuration of the connector determines the number of electrical circuits that can be transmitted through the wiring harness. Knock sensors typically require a two-pin connector, with one pin for the signal wire and the other for the ground wire. -
Facet 3: Connection Mechanism
Connectors utilize different mechanisms to establish a connection. Some connectors employ a locking mechanism that ensures a secure and vibration-resistant connection. Others use a push-to-connect mechanism that allows for quick and easy mating and unmating. -
Facet 4: Environmental Protection
Connectors for wiring harnesses in automotive applications must provide adequate protection against environmental factors. They are designed to withstand exposure to moisture, dust, and extreme temperatures, ensuring reliable operation in all driving conditions.
In conclusion, the connector plays a vital role in the wiring harness for a knock sensor. Its design and construction impact the overall performance and reliability of the knock sensor system. Understanding the different facets of connectors, including their types, pin configuration, connection mechanism, and environmental protection, helps in selecting the appropriate connector for a specific application.
Wire
The wire in a wiring harness for a knock sensor plays a critical role in transmitting electrical signals between the knock sensor and the engine control unit (ECU). These signals are essential for the ECU to monitor and adjust the engine’s performance to prevent knocking, a condition that can damage the engine.
-
Facet 1: Material and Construction
The wire used in a wiring harness for a knock sensor is typically made of copper or aluminum, which are excellent conductors of electricity. The wire’s construction involves stranding multiple thin strands of metal together, which increases flexibility and reduces the risk of breakage due to vibration. -
Facet 2: Gauge and Length
The gauge of the wire, which refers to its thickness, determines its current-carrying capacity. The length of the wire is determined by the distance between the knock sensor and the ECU. -
Facet 3: Insulation and Shielding
The wire is insulated with a material such as PVC or polyethylene to prevent electrical shorts and ensure safe operation. In some cases, the wire may also be shielded with a metallic braid or foil to minimize electromagnetic interference. -
Facet 4: Routing and Protection
The wire is routed through the engine compartment, often bundled with other wires in the wiring harness, and protected from heat, moisture, and abrasion using protective sleeves or conduits.
In conclusion, the wire in a wiring harness for a knock sensor is a crucial component that enables the transmission of electrical signals between the knock sensor and the ECU. Its material, construction, gauge, length, insulation, shielding, routing, and protection all contribute to the overall performance and reliability of the knock sensor system.
Length
The length of a wiring harness for a knock sensor is a critical factor that determines the reach of the wiring harness. The reach refers to the distance between the knock sensor and the engine control unit (ECU) that the wiring harness can span. This distance can vary depending on the vehicle’s make, model, and engine configuration.
An appropriately sized wiring harness ensures that the knock sensor can be positioned correctly for optimal performance. The knock sensor should be placed close to the engine block, typically on the cylinder head or engine block itself, to effectively detect knocking sounds. If the wiring harness is too short, it may not reach the knock sensor, resulting in an incomplete or faulty connection.
Conversely, if the wiring harness is too long, it can create excess slack or loops, which can interfere with other components in the engine compartment. Excess wiring can also be more susceptible to damage from heat, moisture, or abrasion. Therefore, selecting the correct length of the wiring harness is essential to ensure proper installation, functionality, and longevity of the knock sensor system.
In summary, the length of a wiring harness for a knock sensor determines the reach and proper positioning of the knock sensor. Choosing the appropriate length helps ensure optimal performance, prevents connection issues, and minimizes the risk of damage or interference with other components in the engine compartment.
Resistance
In the context of a wiring harness for a knock sensor, resistance plays a crucial role in ensuring the proper functioning and reliability of the system. Resistance refers to the opposition that a material offers to the flow of electrical current. In a wiring harness, the resistance of the wire is a critical factor that can affect the signal transmission between the knock sensor and the engine control unit (ECU).
-
Facet 1: Impact on Signal Strength
The resistance of the wire in a wiring harness can affect the strength of the electrical signal transmitted from the knock sensor to the ECU. Higher resistance can lead to a weaker signal, which may result in reduced sensitivity or accuracy of the knock sensor. This can compromise the ECU’s ability to accurately detect knocking events and adjust the engine’s timing and fuel mixture accordingly.
-
Facet 2: Voltage Drop and Power Loss
Resistance in the wire can cause a voltage drop along the length of the wiring harness. As the electrical current flows through the wire, some of the energy is lost due to resistance, resulting in a decrease in voltage. This voltage drop can affect the performance of the knock sensor, as it may not receive the necessary voltage to operate correctly.
-
Facet 3: Heat Generation and Safety
Excessive resistance in the wire can lead to heat generation due to the dissipation of electrical energy. Overheating of the wire can damage the insulation and compromise the integrity of the wiring harness. In extreme cases, it can even pose a fire hazard.
-
Facet 4: Material and Construction Considerations
The resistance of a wire depends on its material and construction. Different materials have different resistivities, which determine how much they oppose the flow of current. The thickness and length of the wire also influence its resistance. In a wiring harness for a knock sensor, selecting the appropriate wire material and construction is essential to minimize resistance and ensure optimal signal transmission.
In summary, the resistance of the wire in a wiring harness for a knock sensor is a critical factor that impacts signal strength, voltage drop, heat generation, and overall system performance. Understanding the facets of resistance and considering material and construction aspects are crucial for designing and maintaining reliable wiring harnesses that support the effective functioning of knock sensors in automotive applications.
Continuity
In the context of a wiring harness for a knock sensor, continuity is paramount for establishing and maintaining a complete electrical path between the knock sensor and the engine control unit (ECU). Without proper continuity, the electrical signals generated by the knock sensor may not reach the ECU, resulting in incorrect or delayed engine adjustments.
-
Facet 1: Electrical Conductivity
The continuity of a wiring harness relies on the electrical conductivity of its wires. The wire material and construction play a crucial role in ensuring that the electrical signals can flow freely without significant resistance. High-quality wiring harnesses utilize materials with excellent conductivity, such as copper or aluminum, to minimize signal loss and maintain a strong electrical connection.
-
Facet 2: Connection Integrity
Continuity is also influenced by the integrity of the connections within the wiring harness. Proper crimping, soldering, or splicing techniques are essential to create secure and reliable connections between wires and connectors. Loose or faulty connections can disrupt the electrical path and lead to signal interruptions or malfunctions.
-
Facet 3: Insulation and Protection
The insulation surrounding the wires in a wiring harness plays a vital role in maintaining continuity. It prevents electrical shorts and ensures that the current flows through the intended path. High-quality insulation materials, such as PVC or polyethylene, provide excellent protection against moisture, abrasion, and other environmental factors that could compromise continuity.
-
Facet 4: Testing and Maintenance
Regular testing and maintenance are crucial to ensure the continuity of a wiring harness for a knock sensor. Using a multimeter or other diagnostic tools, technicians can check for any breaks, shorts, or resistance issues that may affect signal transmission. Proactive maintenance, such as inspecting the wiring harness for damage or loose connections, can help prevent continuity problems and ensure the reliable operation of the knock sensor system.
In summary, continuity is a fundamental aspect of a wiring harness for a knock sensor, ensuring a complete electrical path for signal transmission. By understanding the facets of electrical conductivity, connection integrity, insulation and protection, and testing and maintenance, technicians can design, install, and maintain wiring harnesses that provide reliable and uninterrupted operation of knock sensor systems in automotive applications.
Shielding
In the context of a wiring harness for a knock sensor, shielding plays a critical role in protecting the sensitive electrical signals from electromagnetic interference (EMI). EMI refers to the disturbance caused by external electromagnetic fields, which can disrupt the proper functioning of electronic components and systems.
EMI can originate from various sources in an automotive environment, such as the ignition system, alternator, or other electrical devices. These sources generate electromagnetic fields that can induce unwanted currents and voltages in the wiring harness, potentially affecting the signal transmission between the knock sensor and the engine control unit (ECU).
Shielding in a wiring harness for a knock sensor typically involves wrapping the wires with a conductive material, such as braided metal or foil. This shield acts as a barrier, preventing external electromagnetic fields from penetrating and interfering with the electrical signals. By maintaining the integrity of the signals, the shielding ensures accurate and reliable communication between the knock sensor and the ECU.
The importance of shielding in a wiring harness for a knock sensor cannot be overstated. Without adequate shielding, EMI can lead to erroneous knock sensor readings, resulting in incorrect engine adjustments and potentially causing engine damage. In severe cases, EMI can even disrupt the operation of the ECU, affecting the overall performance and safety of the vehicle.
In summary, shielding in a wiring harness for a knock sensor is essential for protecting the electrical signals from electromagnetic interference. By mitigating the effects of EMI, shielding ensures the accurate and reliable transmission of signals between the knock sensor and the ECU, contributing to the optimal performance and safety of automotive engines.
Durability
In the context of a wiring harness for a knock sensor, durability is a critical aspect that ensures the reliable functioning of the system in the challenging environment of an engine compartment. The engine compartment is characterized by extreme temperatures, vibrations, moisture, and exposure to chemicals and fluids. A durable wiring harness is essential to withstand these harsh conditions and maintain the integrity of the electrical signals transmitted between the knock sensor and the engine control unit (ECU).
The durability of a wiring harness for a knock sensor is achieved through careful material selection and construction techniques. High-quality wires, connectors, and insulation materials are employed to resist heat, cold, and vibration. The wiring harness is often protected by a rugged outer jacket or conduit that shields it from abrasion and moisture. Additionally, the harness is designed to be flexible enough to withstand the constant movement and vibration within the engine compartment.
The importance of durability in a wiring harness for a knock sensor cannot be understated. A durable harness ensures that the knock sensor can accurately detect knocking sounds and transmit this information to the ECU. This allows the ECU to make timely adjustments to the engine’s timing and fuel mixture, preventing engine damage. Moreover, a durable wiring harness contributes to the overall reliability and longevity of the vehicle’s engine management system.
In summary, durability is a fundamental characteristic of a wiring harness for a knock sensor, enabling it to withstand the harsh conditions of the engine compartment. By understanding the importance of durability and the design considerations involved, engineers and technicians can ensure the and long-lasting performance of knock sensor systems in automotive applications.
Wiring Harness for Knock Sensor
A wiring harness for a knock sensor is a crucial component of a vehicle’s engine management system, responsible for transmitting electrical signals between the knock sensor and the engine control unit (ECU). The knock sensor detects the presence of knocking, an abnormal combustion phenomenon that can damage the engine if left unchecked. The ECU uses the signals from the knock sensor to adjust the engine’s timing and fuel mixture, preventing knocking and optimizing engine performance.
The wiring harness for a knock sensor typically consists of a connector that plugs into the knock sensor, a connector that plugs into the ECU, and a length of wire that connects the two connectors. The wire is made of a conductive material, such as copper or aluminum, and is insulated to prevent electrical shorts. The connectors are designed to create a secure and weatherproof connection between the wiring harness and the knock sensor and the ECU.
A properly functioning wiring harness for a knock sensor is essential for the reliable operation of the engine management system. A faulty wiring harness can lead to inaccurate or delayed signals from the knock sensor, which can result in knocking and potential engine damage. Therefore, it is important to ensure that the wiring harness is in good condition and that the connections are secure.
In summary, a wiring harness for a knock sensor plays a vital role in preventing knocking and optimizing engine performance. By transmitting electrical signals between the knock sensor and the ECU, the wiring harness enables the ECU to make timely adjustments to the engine’s timing and fuel mixture. This ensures smooth engine operation, reduces emissions, and prolongs the life of the engine.
FAQs on Wiring Harness for Knock Sensor
Wiring harnesses for knock sensors play a vital role in ensuring optimal engine performance and preventing costly damage. Here are some frequently asked questions and their answers to provide a deeper understanding of this crucial component:
Question 1: What is the purpose of a wiring harness for a knock sensor?
A wiring harness for a knock sensor facilitates the transmission of electrical signals between the knock sensor and the engine control unit (ECU). These signals relay information about the presence of knocking, an abnormal combustion phenomenon, allowing the ECU to adjust engine timing and fuel mixture to prevent engine damage.
Question 2: What are the key components of a wiring harness for a knock sensor?
A typical wiring harness for a knock sensor consists of three main components: a connector that plugs into the knock sensor, a connector that plugs into the ECU, and a length of wire that connects the two connectors. The wire is made of a conductive material, such as copper or aluminum, and is insulated for safety.
Question 3: Why is the durability of a wiring harness for a knock sensor important?
The durability of the wiring harness is paramount as it needs to withstand the harsh conditions of the engine compartment, including extreme temperatures, vibrations, moisture, and exposure to chemicals. A durable harness ensures reliable signal transmission and protects against potential damage or failure.
Question 4: What are the consequences of a faulty wiring harness for a knock sensor?
A faulty wiring harness can lead to inaccurate or delayed signals from the knock sensor, which can result in knocking and potential engine damage. Knocking can cause premature wear and tear on engine components and, in severe cases, lead to catastrophic engine failure.
Question 5: How can I ensure the proper functioning of the wiring harness for a knock sensor?
To ensure proper functioning, it is essential to regularly inspect the wiring harness for any signs of damage, such as loose connections, fraying, or corrosion. Secure connections and proper insulation are crucial for maintaining optimal signal transmission.
Question 6: When should I consider replacing the wiring harness for a knock sensor?
If the wiring harness exhibits signs of significant damage or if the knock sensor is not functioning correctly despite other troubleshooting measures, it may be necessary to replace the wiring harness. A qualified mechanic can assess the condition of the harness and make the appropriate recommendation.
In summary, understanding the importance and proper maintenance of a wiring harness for a knock sensor is crucial for ensuring optimal engine performance and longevity. Regular inspections and prompt replacement when necessary contribute to the overall health and reliability of your vehicle.
Transition to the next article section:
For further insights into the intricacies of wiring harnesses for knock sensors, explore our comprehensive article on the subject, where we delve deeper into its design, installation, and troubleshooting.
Conclusion
In conclusion, the wiring harness for a knock sensor plays a critical role in ensuring optimal engine performance and preventing costly damage. Its primary function of transmitting electrical signals between the knock sensor and the engine control unit (ECU) enables the ECU to make timely adjustments to engine timing and fuel mixture, thereby preventing knocking and optimizing engine operation.
Understanding the key components, importance, and proper maintenance of a wiring harness for a knock sensor is essential for ensuring the longevity and reliability of your vehicle. Regular inspections, secure connections, and prompt replacement when necessary contribute to a well-functioning engine management system.
As technology continues to advance, the design and functionality of wiring harnesses for knock sensors may evolve. However, their fundamental role in preventing knocking and optimizing engine performance will remain crucial for the foreseeable future. By staying informed and engaging in proper maintenance practices, you can ensure that your vehicle’s engine operates at its best for many years to come.
Youtube Video:
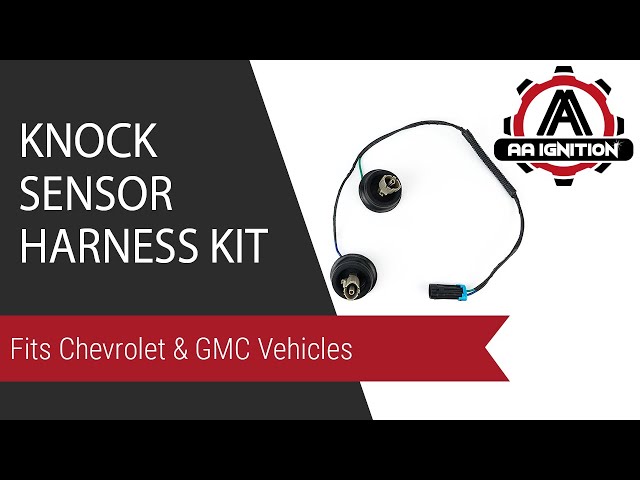