Rewiring a Zero Turn Mower Without an Original Wiring Harness
Rewiring a zero turn mower without an original wiring harness can be a daunting task, but it is possible with the right tools and materials. By following these steps, you can create a new wiring harness that will get your mower up and running again.
Materials:
- Wire (14-16 gauge)
- Wire connectors
- Electrical tape
- Heat shrink tubing
- Crimping tool
- Wire strippers
Steps:
- Identify the electrical components that need to be wired.
- Determine the wire gauge and length needed for each component.
- Cut the wire to the correct length and strip the ends.
- Connect the wires to the electrical components using wire connectors.
- Wrap the wire connections with electrical tape.
- Cover the wire connections with heat shrink tubing.
- Route the wires neatly and securely.
- Test the wiring harness to make sure it is working properly.
Benefits of Rewiring a Zero Turn Mower Without an Original Wiring Harness:
- Can save money by avoiding the cost of a new wiring harness.
- Can be customized to meet your specific needs.
- Can improve the performance of your mower.
By following these steps, you can successfully rewire a zero turn mower without an original wiring harness. This can be a rewarding project that can save you money and improve the performance of your mower.
Essential Aspects of Rewiring a Zero Turn Mower Without an Original Wiring Harness
Rewiring a zero turn mower without an original wiring harness requires careful consideration of several key aspects. These aspects encompass various dimensions of the task, from understanding the electrical components to ensuring proper installation and safety.
- Electrical Components: Identify the essential electrical components that need to be connected, such as the ignition switch, starter solenoid, and battery.
- Wire Gauge: Determine the appropriate wire gauge for each component based on its current draw to ensure adequate power delivery.
- Wire Length: Measure and cut the wires to the correct length to avoid excess or insufficient wiring.
- Wire Connectors: Choose the right wire connectors, such as crimp connectors or solderless terminals, to ensure secure and reliable connections.
- Electrical Tape: Insulate and protect wire connections using high-quality electrical tape.
- Heat Shrink Tubing: Provide additional protection and strain relief to wire connections by covering them with heat shrink tubing.
- Routing and Securing: Route the wires neatly and securely to prevent damage and ensure proper operation of the mower.
Understanding these key aspects is crucial for a successful rewiring project. Proper identification of electrical components, selection of appropriate wire gauge and connectors, and careful routing and securing of wires ensure the safe and efficient operation of the zero turn mower.
Electrical Components
Identifying the essential electrical components and understanding their connections is crucial when rewiring a zero turn mower without an original wiring harness. These components form the core of the mower’s electrical system and are responsible for starting, running, and controlling the machine.
The ignition switch provides power to the starter solenoid, which in turn engages the starter motor to start the engine. The battery supplies electrical energy to the entire system and must be properly connected to ensure reliable operation. Additionally, other components like safety switches, sensors, and lights need to be identified and connected correctly.
By understanding the function and interconnections of these electrical components, you can create a new wiring harness that will restore the mower’s functionality. This involves tracing the original wiring paths, identifying the correct wire colors and gauges, and ensuring secure and insulated connections.
Proper identification and connection of electrical components is essential for the safe and efficient operation of the zero turn mower. It allows the electrical system to provide power, control, and safety features, enabling the mower to perform its intended functions.
Wire Gauge
When rewiring a zero turn mower without an original wiring harness, determining the appropriate wire gauge is crucial to ensure the proper functioning of the electrical system. Wire gauge refers to the thickness of the wire, which directly affects its current-carrying capacity.
- Electrical Components and Current Draw: Different electrical components in the mower, such as the starter motor, ignition coil, and lights, have varying current draw requirements. It is essential to identify these requirements to select the appropriate wire gauge.
- Power Delivery and Voltage Drop: The wire gauge should be adequate to handle the current draw of the component without excessive voltage drop. Insufficient wire gauge can lead to voltage loss, resulting in reduced power delivery and potential damage to components.
- Wire Resistance and Heat Dissipation: Thinner wires have higher resistance, which can cause heat buildup and energy loss. Choosing the correct wire gauge ensures that the wire can safely dissipate heat, preventing overheating and potential fire hazards.
By understanding the relationship between wire gauge, current draw, and power delivery, you can select the appropriate wire gauge for each component in the zero turn mower’s electrical system. This ensures that the mower operates efficiently and safely, minimizing the risk of electrical problems.
Wire Length
Determining the correct wire length is a critical aspect of rewiring a zero turn mower without an original wiring harness. It directly affects the mower’s electrical performance, safety, and ease of use.
Excess Wiring: Excessive wiring can create clutter, increase the risk of tangles and snags, and potentially lead to electrical shorts. Excess wire also adds unnecessary weight to the mower, affecting its maneuverability and efficiency.
Insufficient Wiring: Wires that are too short can create strain on connections, leading to loose or broken wires. This can result in intermittent electrical problems, reduced power delivery, and even safety hazards.
Measuring and cutting the wires to the correct length ensures that each component has sufficient wire to reach its connection point without excess. This optimizes the electrical system, reduces the risk of problems, and improves the overall functionality of the mower.
Additionally, proper wire length facilitates easier installation and maintenance. Wires that are cut to the correct length can be routed neatly, avoiding tangles and making it easier to troubleshoot any future electrical issues.
By understanding the importance of wire length and following proper measurement and cutting techniques, you can create a reliable and efficient wiring harness for your zero turn mower.
Wire Connectors
When rewiring a zero turn mower without an original wiring harness, selecting the right wire connectors is crucial for establishing secure and reliable electrical connections. Wire connectors play a vital role in maintaining the integrity of the electrical system and preventing potential electrical issues.
Electrical Safety and Reliability: Loose or poorly connected wires can lead to electrical shorts, arcing, and even fires. Using the appropriate wire connectors ensures a secure and stable connection between wires, minimizing the risk of these hazards and ensuring the safe operation of the mower.
Voltage Drop and Power Delivery: Properly crimped or soldered wire connectors provide a low-resistance path for electrical current to flow. This minimizes voltage drop and ensures that electrical components receive the necessary power to operate efficiently.
Ease of Installation and Maintenance: Crimp connectors and solderless terminals allow for quick and easy installation, reducing the time and effort required to rewire the mower. They also simplify future maintenance or troubleshooting by providing easily accessible and reliable connection points.
Understanding the significance of wire connectors and using the right type for each connection is essential for a successful rewiring project. By ensuring secure and reliable connections, you can minimize electrical problems, improve the performance of the mower, and ensure its safe and efficient operation.
Electrical Tape
In the context of rewiring a zero turn mower without an original wiring harness, electrical tape plays a crucial role in ensuring the safety, reliability, and longevity of the electrical system. Its primary function is to insulate and protect wire connections, preventing electrical shorts, arcing, and other potential hazards.
When electrical wires are connected, bare conductors can come into contact, creating a path for unintended current flow. This can lead to short circuits, which can damage electrical components, cause overheating, and even pose a fire risk. Electrical tape provides a non-conductive barrier over these connections, preventing such occurrences.
Furthermore, electrical tape protects wire connections from environmental factors such as moisture, dust, and corrosion. These elements can degrade the connection over time, leading to increased resistance, voltage drop, and potential failure. The insulating properties of electrical tape prevent these contaminants from reaching the connection, ensuring a reliable and long-lasting electrical system.
Using high-quality electrical tape is essential to achieve these benefits. Inferior tape may not provide adequate insulation or protection, compromising the safety and reliability of the electrical system. By investing in high-quality electrical tape and applying it properly, you can ensure that your zero turn mower’s electrical connections are secure, protected, and operating at their best.
Heat Shrink Tubing
In the context of rewiring a zero turn mower without an original wiring harness, heat shrink tubing plays a vital role in enhancing the durability, reliability, and safety of the electrical system. Its primary function is to provide additional protection and strain relief to wire connections, complementing the insulation provided by electrical tape.
When electrical wires are connected, they are subjected to various environmental factors and mechanical stresses. Heat shrink tubing offers several benefits that address these challenges:
- Environmental Protection: Heat shrink tubing creates a protective barrier around wire connections, shielding them from moisture, dust, dirt, and other contaminants. This prevents corrosion, oxidation, and insulation breakdown, ensuring long-lasting electrical connections.
- Strain Relief: Heat shrink tubing provides mechanical support and strain relief to wire connections. It reduces the stress on solder joints and crimps, preventing wires from breaking or becoming loose due to vibration or movement.
- Insulation Enhancement: Heat shrink tubing provides an additional layer of insulation over electrical tape, enhancing the overall protection against electrical shorts and arcing. This is particularly important in high-voltage or high-current applications.
Using heat shrink tubing is a simple and effective way to improve the reliability and longevity of electrical connections in a zero turn mower. It is a crucial component of a well-repaired wiring harness, ensuring that the mower operates safely and efficiently for years to come.
Routing and Securing
In the context of rewiring a zero turn mower without an original wiring harness, routing and securing the wires plays a crucial role in ensuring the mower’s safety, reliability, and performance.
- Organized Wiring: Neatly routed and secured wires prevent tangles and clutter, which can lead to accidental damage or disconnections. This organization also simplifies future maintenance or troubleshooting by making it easier to trace and access wires.
- Protection from Damage: Proper routing and securing protect wires from external factors such as abrasion, heat, and moisture. By keeping wires away from moving parts, sharp edges, and potential sources of heat, their lifespan is extended, reducing the risk of electrical failures.
- Strain Relief: Securing wires at regular intervals provides strain relief, preventing excessive tension or movement that could damage connections. This is especially important in areas where wires are subject to vibration or flexing.
- Heat Dissipation: Routing wires with sufficient spacing allows for proper heat dissipation. Overcrowded or bundled wires can trap heat, leading to insulation damage and potential electrical hazards.
By following proper routing and securing techniques, you can ensure that the electrical system of your zero turn mower operates safely, efficiently, and without disruptions. This contributes to the overall reliability and longevity of the mower, reducing the likelihood of electrical problems and costly repairs.
Rewiring a Zero Turn Mower Without an Original Wiring Harness
Rewiring a zero turn mower without an original wiring harness involves replacing the existing electrical wiring system with a new one, typically due to damage or malfunction of the original harness. This task requires a thorough understanding of electrical systems and careful attention to detail to ensure the mower operates safely and efficiently.
Replacing the wiring harness provides several benefits, including:
- Improved safety: A new wiring harness eliminates the risk of electrical shorts or malfunctions that could lead to accidents.
- Enhanced performance: A properly wired mower ensures that all electrical components receive the necessary power, leading to optimal performance.
- Increased reliability: A new wiring harness reduces the likelihood of electrical problems, resulting in fewer breakdowns and a longer lifespan for the mower.
To begin the rewiring process, gather the necessary tools and materials, including wire, connectors, electrical tape, heat shrink tubing, and a crimping tool. It is also helpful to have a wiring diagram for your specific mower model.
FAQs
Question 1: Is it possible to rewire a zero turn mower without the original wiring harness?
Answer: Yes, it is possible to rewire a zero turn mower without the original wiring harness. However, this task requires a thorough understanding of electrical systems and careful attention to detail to ensure the mower operates safely and efficiently.
Question 2: What are the benefits of replacing the wiring harness on a zero turn mower?
Answer: Replacing the wiring harness provides several benefits, including improved safety, enhanced performance, and increased reliability.
Question 3: What tools and materials are needed to rewire a zero turn mower?
Answer: To rewire a zero turn mower, you will need wire, connectors, electrical tape, heat shrink tubing, a crimping tool, and a wiring diagram for your specific mower model.
Question 4: How do I determine the correct wire gauge to use when rewiring my zero turn mower?
Answer: The appropriate wire gauge depends on the current draw of the electrical components being connected. Refer to the wiring diagram or consult an electrician for guidance.
Question 5: What type of connectors should I use to connect the wires?
Answer: Use high-quality wire connectors that are suitable for the wire gauge and application. Crimp connectors or solderless terminals are commonly used for electrical connections.
Question 6: How do I ensure the new wiring harness is properly routed and secured?
Answer: Route the wires neatly and securely to prevent damage and ensure proper operation. Use zip ties or other suitable methods to secure the wires and protect them from abrasion or heat.
Remember, rewiring a zero turn mower without an original wiring harness requires technical expertise and attention to detail. If you are not confident in your abilities, it is recommended to seek professional assistance from a qualified electrician.
Transition to the next article section…
Conclusion
Rewiring a zero turn mower without an original wiring harness is a complex task that requires careful planning, technical expertise, and attention to detail. This comprehensive guide has provided a thorough overview of the process, from understanding electrical components and selecting the appropriate wire gauge to routing and securing the new wiring harness. By following these steps and adhering to safety precautions, you can successfully restore the electrical functionality of your mower.
Remember, electrical work can be hazardous, and it is crucial to prioritize safety throughout the rewiring process. If you lack experience or confidence in your abilities, do not hesitate to seek assistance from a qualified electrician. A professionally installed wiring harness will ensure the safe and reliable operation of your zero turn mower for years to come.
As you embark on this rewiring project, approach it with patience and a commitment to doing it right. By following the guidance provided in this article and taking the necessary precautions, you can restore your mower to its former glory and enjoy the satisfaction of a job well done.
Youtube Video:
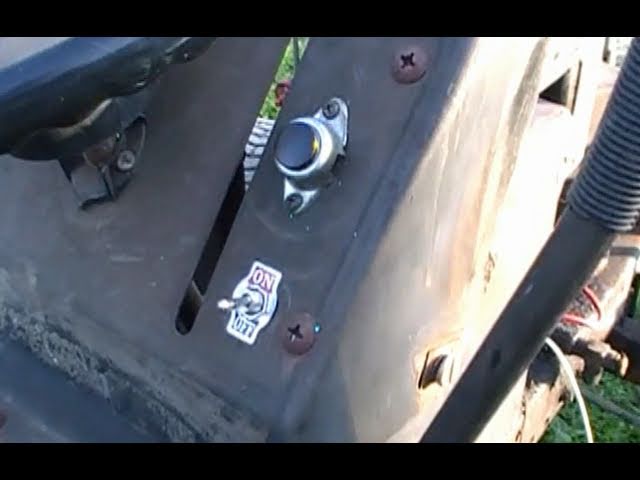