Electric Connectors for Wiring
Electric connectors are essential components in electrical wiring, providing a secure and reliable connection between two or more conductors. They come in various shapes, sizes, and materials, and choosing the right connector for the job is crucial for ensuring the safety and functionality of the electrical system.
To help you understand the different types of electric connectors available and how to create them, we’ve put together a comprehensive chart and diagram guide. This guide covers the most common types of connectors used in electrical wiring, their applications, and step-by-step instructions on how to create them.
Benefits of using a chart or diagram to create electric connectors for wiring:
- Provides a visual reference for the different types of connectors available
- Helps you choose the right connector for the job
- Provides step-by-step instructions on how to create each type of connector
- Saves time and effort by eliminating the need to search for information from multiple sources
Conclusion:
By using a chart or diagram to create electric connectors for wiring, you can ensure that your electrical connections are safe, reliable, and code-compliant. The examples and guidelines provided in this guide will help you choose the right connector for the job and create it correctly.
Electric Connectors for Wiring
Electric connectors play a crucial role in electrical wiring, ensuring secure and reliable connections between conductors. Here are six key aspects to consider when working with electric connectors for wiring:
- Type: Various types of connectors are available, each with its own applications and advantages.
- Material: Connectors can be made from different materials, such as copper, brass, or plastic, affecting their conductivity and durability.
- Size: Connectors come in a range of sizes, which must match the wire gauge being used.
- Insulation: Connectors are often insulated to prevent electrical shock and short circuits.
- Termination: Connectors can be terminated in various ways, such as soldering, crimping, or screw terminals.
- Compliance: Connectors should meet industry standards and codes to ensure safety and reliability.
These key aspects are interconnected and must be considered together when selecting and using electric connectors for wiring. For example, the type of connector will determine the material, size, and termination method that is appropriate. By understanding these aspects, you can choose the right connectors for your specific wiring needs and ensure a safe and reliable electrical system.
Type
In the context of electric connectors for wiring, the type of connector plays a crucial role in determining its suitability for a specific application. Different types of connectors have unique characteristics, advantages, and applications, making it essential to understand the available options.
- Screw terminals: Screw terminals are commonly used in electrical wiring due to their ease of installation and maintenance. They consist of a screw that clamps down on the wire, creating a secure connection. Screw terminals are ideal for applications where frequent access and adjustments may be required.
- Crimp connectors: Crimp connectors are another popular type of connector used in electrical wiring. They are installed using a crimping tool that permanently deforms the connector around the wire, creating a gas-tight connection. Crimp connectors are compact, reliable, and suitable for high-vibration environments.
- Solder connectors: Solder connectors are formed by soldering the wire directly to the connector. They offer a permanent and highly conductive connection, making them suitable for applications where a secure and low-resistance connection is critical. However, solder connectors require specialized tools and skills to install.
- Push-in connectors: Push-in connectors provide a convenient and time-saving method of connecting wires. They feature a spring-loaded mechanism that allows the wire to be inserted without the need for tools. Push-in connectors are ideal for applications where quick and easy connections are required.
Understanding the different types of electric connectors for wiring and their respective advantages allows you to select the most appropriate connector for your specific needs, ensuring a safe, reliable, and efficient electrical connection.
Material
The material of electric connectors for wiring significantly impacts their performance and suitability for various applications. Different materials offer unique advantages and drawbacks, influencing the connector’s conductivity, durability, and overall reliability.
- Conductivity: The material of the connector affects its ability to conduct electricity. Copper is an excellent conductor, making it a popular choice for electrical connectors. Brass and plastic, on the other hand, have lower conductivity but may be suitable for specific applications.
- Durability: The material of the connector also affects its durability and resistance to wear and tear. Copper and brass are relatively durable materials, while plastic connectors may be more susceptible to damage in harsh environments.
- Corrosion resistance: The material of the connector should be resistant to corrosion, especially in environments with moisture or chemicals. Copper and brass have good corrosion resistance, while plastic connectors may require additional protection.
- Temperature resistance: The material of the connector should be able to withstand the operating temperatures of the electrical system. Copper and brass have high melting points, while plastic connectors may have lower temperature limits.
By carefully considering the material of the electric connectors for wiring, you can ensure that they meet the specific requirements of your application and provide a reliable and long-lasting connection.
Size
The size of electric connectors for wiring is a critical factor that directly impacts the safety and reliability of the electrical connection. The size of the connector must match the wire gauge being used to ensure proper current carrying capacity and avoid overheating or damage to the connector and wire.
When the connector size is too small for the wire gauge, it can lead to loose connections, arcing, and potential fire hazards. Conversely, using a connector that is too large for the wire gauge can result in a weak connection, increased resistance, and power loss.
Therefore, it is essential to carefully select the correct connector size based on the wire gauge being used. This ensures a secure and reliable connection that meets the electrical requirements of the application. Understanding the relationship between connector size and wire gauge is crucial for proper electrical wiring and the prevention of potential electrical hazards.
Insulation
Insulation plays a critical role in electric connectors for wiring, ensuring the safety and reliability of electrical systems. By preventing electrical shock and short circuits, insulation safeguards both personnel and equipment.
- Protection against electrical shock: Insulation provides a protective barrier around the connector, preventing accidental contact with live electrical components. This is especially important in areas where people may come into contact with the connectors, such as in homes, offices, and industrial settings.
- Prevention of short circuits: Insulation helps prevent short circuits by separating conductors from each other and from other conductive surfaces. Short circuits occur when current takes an unintended path, potentially leading to overheating, damage to equipment, and even fires.
- Maintenance of electrical integrity: Insulation helps maintain the electrical integrity of the connection by preventing current leakage and ensuring that electricity flows through the intended path. This is crucial for the proper functioning of electrical systems and the prevention of power loss.
- Durability and reliability: Insulation protects the connector from environmental factors such as moisture, dust, and chemicals. This enhances the durability and reliability of the connector, ensuring long-term performance and reducing the risk of premature failure.
In summary, insulation is a vital component of electric connectors for wiring, providing protection against electrical shock, preventing short circuits, maintaining electrical integrity, and enhancing durability. By understanding the importance of insulation, you can ensure the safety and reliability of your electrical connections.
Termination
Termination is an essential aspect of electric connectors for wiring, as it establishes a secure and reliable connection between the connector and the wire.
- Soldering: Soldering involves joining the connector and wire using a metal alloy with a lower melting point than the connector. When heated, the solder melts and flows into the joint, creating a permanent bond. Soldering provides a strong and durable connection, but it requires specialized tools and skills.
- Crimping: Crimping involves using a crimping tool to compress a metal sleeve or ferrule around the connector and wire. This creates a gas-tight connection that prevents corrosion and ensures a secure electrical contact. Crimping is a reliable and efficient termination method, suitable for high-vibration environments.
- Screw terminals: Screw terminals provide a convenient and reusable method of terminating connectors. They consist of a screw that clamps down on the wire, creating a secure connection. Screw terminals are commonly used in electrical installations where frequent access and adjustments may be required.
The choice of termination method depends on factors such as the type of connector, wire gauge, and application requirements. By understanding the different termination methods available, you can ensure a reliable and long-lasting connection for your electric connectors for wiring.
Compliance
In the context of electric connectors for wiring, compliance with industry standards and codes is paramount for ensuring the safety and reliability of electrical installations. By adhering to these standards and codes, manufacturers and users can minimize the risk of electrical hazards, fires, and accidents.
- Safety: Industry standards and codes incorporate stringent safety requirements for electric connectors for wiring. These requirements address factors such as insulation, current carrying capacity, and materials used. By meeting these standards, manufacturers ensure that their connectors are safe to use and minimize the risk of electrical shocks, short circuits, and fires.
- Reliability: Compliance with industry standards and codes helps ensure the reliability of electric connectors for wiring. These standards specify performance requirements, such as durability, resistance to corrosion, and temperature variations. By meeting these requirements, manufacturers produce connectors that can withstand the rigors of real-world applications and provide long-lasting performance.
- Compatibility: Industry standards and codes promote compatibility between different types of electric connectors for wiring. By adhering to these standards, manufacturers ensure that their connectors can be used with a wide range of electrical components and systems. This simplifies installation, maintenance, and upgrades, saving time and effort.
- Legal requirements: In many jurisdictions, it is a legal requirement to use electric connectors for wiring that comply with industry standards and codes. Failure to comply can result in fines, penalties, or even criminal charges in the event of an accident or electrical hazard.
Overall, compliance with industry standards and codes is essential for ensuring the safety, reliability, and compatibility of electric connectors for wiring. By adhering to these standards, manufacturers and users can minimize risks, improve performance, and ensure the safe and efficient operation of electrical systems.
Electrical connectors, the unsung heroes of the electrical world, play a pivotal role in wiring, ensuring a secure and efficient flow of electricity. These remarkable devices bridge the gap between electrical wires, components, and systems, creating a seamless network that powers our modern lives.
The importance of electric connectors for wiring cannot be overstated. They ensure the safe and reliable transmission of electricity, preventing short circuits, fires, and other electrical hazards. By providing a secure connection, connectors minimize power loss and maintain the integrity of electrical systems, ensuring optimal performance and longevity.
Electric connectors for wiring have evolved over time, adapting to the ever-changing demands of the electrical industry. From simple screw terminals to advanced push-in connectors, these devices have become more compact, efficient, and user-friendly.
As we delve deeper into the world of electric connectors for wiring, we will explore their types, materials, sizes, insulation, termination methods, and compliance requirements. Understanding these aspects will empower you to make informed decisions when selecting and using connectors, ensuring the safety, reliability, and efficiency of your electrical systems.
FAQs on Electric Connectors for Wiring
Electric connectors for wiring play a crucial role in ensuring the safety and reliability of electrical systems. Here are some frequently asked questions and their answers to help you better understand and use these essential components:
Question 1: What are the different types of electric connectors for wiring?
Electric connectors come in various types, including screw terminals, crimp connectors, solder connectors, and push-in connectors. Each type has its own advantages and applications, and the choice depends on factors such as the wire gauge, current carrying capacity, and environmental conditions.
Question 2: What is the best material for electric connectors?
The best material for electric connectors depends on the specific application. Copper is a popular choice due to its excellent conductivity and durability. Brass and plastic are also used, offering good conductivity and corrosion resistance, respectively.
Question 3: How do I choose the right size of electric connector?
The size of the electric connector should match the wire gauge being used. Using a connector that is too small can lead to loose connections and overheating, while using a connector that is too large can result in a weak connection and increased resistance.
Question 4: Why is insulation important for electric connectors?
Insulation is crucial for electric connectors as it prevents electrical shock, short circuits, and current leakage. It also protects the connector from environmental factors such as moisture, dust, and chemicals.
Question 5: What are the different termination methods for electric connectors?
Electric connectors can be terminated using various methods, including soldering, crimping, and screw terminals. The choice of termination method depends on the type of connector, wire gauge, and application requirements.
Question 6: Why is compliance with industry standards important for electric connectors?
Compliance with industry standards ensures that electric connectors meet specific safety and performance requirements. It helps prevent electrical hazards, fires, and accidents, and also ensures compatibility with other electrical components and systems.
By understanding these frequently asked questions, you can make informed decisions when selecting and using electric connectors for wiring, ensuring the safety, reliability, and efficiency of your electrical systems.
Transitioning to the next article section…
Conclusion
Electric connectors for wiring play a critical role in the safety, reliability, and efficiency of electrical systems. This comprehensive guide has explored the different types of connectors, their materials, sizes, insulation, termination methods, and compliance requirements, providing you with a solid understanding of these essential components.
By carefully selecting and using the right electric connectors for wiring, you can ensure that your electrical systems operate safely, reliably, and efficiently. Remember, these connectors are the unsung heroes of the electrical world, silently ensuring the seamless flow of electricity that powers our modern lives. As technology continues to advance, we can expect further innovations in electric connectors, making them even more compact, efficient, and user-friendly.
Youtube Video:
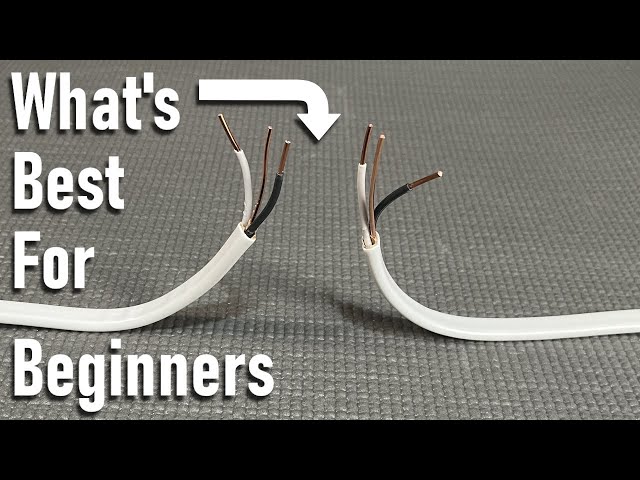