Computer Wiring Harness for DD15 Engine Keyword Chart or Diagram
A computer wiring harness is a crucial component of the DD15 engine, responsible for transmitting electrical signals and power throughout the engine system. It plays a vital role in ensuring optimal engine performance, reliability, and safety.
To effectively create a computer wiring harness for a DD15 engine, it is essential to follow specific steps and guidelines. The following chart outlines the key steps involved:
Step | Description |
---|---|
1 | Gather necessary materials and tools, including wires, connectors, terminals, and a wiring diagram. |
2 | Study the wiring diagram thoroughly to understand the electrical system and the connections required. |
3 | Cut and strip the wires to the appropriate lengths and prepare them for termination. |
4 | Crimp the terminals onto the wire ends using a proper crimping tool. |
5 | Insert the terminals into the connectors and secure them. |
6 | Route the wiring harness through the engine compartment, following the designated paths. |
7 | Secure the wiring harness using cable ties or other appropriate methods to prevent damage. |
8 | Test the wiring harness for continuity and proper electrical connections. |
Benefits of Using a Computer Wiring Harness Chart or Diagram:
- Provides a clear visual representation of the wiring system, making it easier to understand and troubleshoot.
- Helps ensure accurate and efficient wiring, reducing the risk of errors and malfunctions.
- Serves as a valuable reference guide for maintenance and repair purposes.
- Facilitates collaboration and knowledge sharing among technicians.
In conclusion, effectively creating a computer wiring harness for a DD15 engine requires careful planning and adherence to specific guidelines. By utilizing a wiring harness chart or diagram, engineers and technicians can ensure the accuracy, reliability, and efficiency of the electrical system, contributing to the overall performance and longevity of the engine.
Essential Aspects of Computer Wiring Harness for DD15 Engine
A computer wiring harness is a critical component of the DD15 engine, responsible for transmitting electrical signals and power throughout the engine system. It plays a vital role in ensuring optimal engine performance, reliability, and safety. Understanding the essential aspects of a computer wiring harness for a DD15 engine is crucial for its effective design, installation, and maintenance.
- Connectivity: The wiring harness provides electrical connections between various engine components, including sensors, actuators, and the engine control module.
- Signal Transmission: It enables the transmission of electrical signals, carrying data and commands throughout the engine system.
- Power Distribution: The wiring harness distributes electrical power to various engine components, ensuring their proper operation.
- Reliability: A well-designed and installed wiring harness contributes to the overall reliability of the engine by preventing electrical faults and malfunctions.
- Durability: The wiring harness must be durable enough to withstand the harsh operating conditions of an engine, including vibrations, temperature extremes, and exposure to chemicals.
- Maintainability: Proper design and documentation of the wiring harness facilitate easy maintenance and troubleshooting, reducing downtime and maintenance costs.
In conclusion, the essential aspects of a computer wiring harness for a DD15 engine encompass its connectivity, signal transmission, power distribution, reliability, durability, and maintainability. Addressing these aspects ensures the efficient and reliable operation of the engine, contributing to its overall performance and longevity.
Connectivity
In the context of a computer wiring harness for a DD15 engine, connectivity plays a crucial role in ensuring optimal engine performance and reliability. The wiring harness serves as the backbone of the electrical system, facilitating communication between various engine components, including sensors, actuators, and the engine control module (ECM).
- Electrical Connections: The wiring harness provides a network of electrical connections, allowing sensors to transmit data to the ECM, actuators to receive commands from the ECM, and the ECM to control engine functions.
- Signal Transmission: The wiring harness enables the transmission of electrical signals, carrying vital information such as engine speed, temperature, and fuel pressure to the ECM for processing and decision-making.
- Power Distribution: In addition to signal transmission, the wiring harness also distributes electrical power to various engine components, ensuring their proper operation.
- Redundancy and Fault Tolerance: The wiring harness often incorporates redundancy and fault tolerance measures, such as multiple connections or backup circuits, to minimize the impact of potential electrical failures.
Overall, the connectivity aspect of a computer wiring harness for a DD15 engine is essential for maintaining seamless communication and control within the engine system, contributing to its overall efficiency, performance, and reliability.
Signal Transmission
Signal transmission is a critical aspect of a computer wiring harness for a DD15 engine, as it facilitates the exchange of vital information and commands within the engine system. The wiring harness serves as a network of electrical pathways, allowing sensors to transmit data to the engine control module (ECM), and for the ECM to send commands to actuators and other engine components.
The data transmitted through the wiring harness includes engine speed, temperature, fuel pressure, and other parameters. This information is crucial for the ECM to make informed decisions regarding engine operation, such as adjusting fuel injection timing or ignition timing. The wiring harness also transmits commands from the ECM to actuators, controlling functions such as valve timing, turbocharger boost, and exhaust gas recirculation.
The reliable transmission of signals is essential for the proper functioning of the DD15 engine. Faulty or damaged wiring can lead to incorrect data transmission or loss of communication, resulting in engine performance issues, reduced fuel efficiency, and potential safety hazards. Therefore, the design and construction of the wiring harness must prioritize signal integrity, noise immunity, and protection against electromagnetic interference.
In summary, the signal transmission capability of a computer wiring harness for a DD15 engine is vital for maintaining optimal engine performance, reliability, and safety. By ensuring reliable and accurate signal transmission, the wiring harness contributes to the efficient operation and control of the engine system.
Power Distribution
Power distribution is a critical aspect of a computer wiring harness for a DD15 engine, as it ensures that all electrical components receive the necessary power to operate correctly. The wiring harness serves as a network of electrical pathways, distributing power from the battery and other power sources to various engine components, such as sensors, actuators, and the engine control module (ECM).
The reliable distribution of power is essential for the proper functioning of the DD15 engine. Without a properly functioning wiring harness, electrical components may not receive sufficient power, leading to malfunctions, reduced performance, or even complete failure of the engine system. For example, if the fuel injectors do not receive adequate power, the engine may not be able to maintain proper fuel injection timing, resulting in poor combustion and reduced engine efficiency.
The design and construction of the wiring harness must prioritize the efficient and safe distribution of power. The wiring harness must be able to handle the electrical loads of all connected components without excessive voltage drop or power loss. Additionally, the wiring harness must be protected against short circuits and other electrical faults that could damage components or cause a fire.
In summary, the power distribution capability of a computer wiring harness for a DD15 engine is vital for maintaining optimal engine performance, reliability, and safety. By ensuring reliable and efficient power distribution, the wiring harness contributes to the smooth operation and control of the engine system.
Reliability
The reliability of a computer wiring harness for a DD15 engine is of paramount importance, as it directly impacts the overall reliability and performance of the engine. A well-designed and installed wiring harness plays a crucial role in preventing electrical faults and malfunctions that can lead to engine problems, downtime, and safety hazards.
Electrical faults can arise from various causes, such as poor connections, damaged insulation, or exposure to harsh environmental conditions. These faults can disrupt signal transmission, power distribution, or both, leading to engine control issues, component failures, or even engine shutdown. A reliable wiring harness minimizes the risk of such faults by ensuring secure connections, proper insulation, and protection against environmental factors.
By preventing electrical faults and malfunctions, a reliable wiring harness contributes to the overall reliability of the DD15 engine in several ways:
- Reduced Downtime: Electrical faults can cause unexpected engine failures, resulting in costly downtime for maintenance and repairs. A reliable wiring harness helps prevent these failures, ensuring that the engine remains operational and minimizing downtime.
- Improved Performance: Electrical faults can interfere with engine control and component operation, leading to reduced engine performance and efficiency. A reliable wiring harness ensures that all engine components receive the necessary power and signals, resulting in optimal engine performance.
- Enhanced Safety: Electrical faults can potentially lead to safety hazards, such as fires or electrical shocks. A reliable wiring harness minimizes these risks by preventing electrical faults and ensuring that the electrical system operates safely.
In conclusion, the reliability of a computer wiring harness for a DD15 engine is a critical factor in maintaining engine performance, reducing downtime, and ensuring safety. By preventing electrical faults and malfunctions, a well-designed and installed wiring harness contributes significantly to the overall reliability of the engine.
Durability
In the context of a computer wiring harness for a DD15 engine, durability is of paramount importance due to the harsh operating conditions in which the engine operates. The wiring harness must be able to withstand extreme temperatures, vibrations, and exposure to chemicals to ensure reliable and safe engine operation.
The durability of the wiring harness is vital for several reasons:
- Extreme Temperatures: DD15 engines operate in a wide range of temperatures, from freezing cold to extreme heat. The wiring harness must be able to withstand these temperature variations without becoming brittle or melting, ensuring proper electrical connections and signal transmission.
- Vibrations: Engines produce significant vibrations during operation. The wiring harness must be able to withstand these vibrations without becoming loose or damaged, preventing electrical faults and ensuring reliable engine performance.
- Chemical Exposure: The engine compartment is exposed to various chemicals, such as oil, fuel, and coolant. The wiring harness must be resistant to these chemicals to prevent corrosion and damage to the insulation, maintaining electrical integrity.
To achieve durability, computer wiring harnesses for DD15 engines are typically constructed using high-quality materials and manufacturing processes. The wires are often made of durable materials like copper or aluminum, and the insulation is designed to withstand extreme temperatures and chemical exposure. Additionally, the wiring harness is often secured using vibration-resistant mounting methods to prevent damage from engine vibrations.
In summary, the durability of a computer wiring harness for a DD15 engine is critical for ensuring reliable engine operation in harsh operating conditions. By using durable materials, construction methods, and mounting techniques, the wiring harness can withstand extreme temperatures, vibrations, and chemical exposure, contributing to the overall longevity and performance of the engine.
Maintainability
Maintainability is a crucial aspect of a computer wiring harness for a DD15 engine, as it directly impacts the ease and cost of maintaining and repairing the engine. A well-designed and documented wiring harness simplifies maintenance tasks, reduces troubleshooting time, and minimizes downtime, leading to lower maintenance costs and increased engine uptime.
Here’s how maintainability contributes to the effectiveness of a computer wiring harness for a DD15 engine:
- Easy Maintenance: A well-designed wiring harness allows for easy access to connectors, terminals, and other components, making it simpler to perform maintenance tasks such as inspections, cleaning, and repairs. This ease of maintenance reduces the time and effort required for servicing the engine, resulting in lower labor costs.
- Efficient Troubleshooting: Proper documentation, including wiring diagrams and schematics, enables technicians to quickly identify and resolve electrical issues. By providing a clear understanding of the wiring harness layout and connections, the documentation reduces troubleshooting time and minimizes the risk of misdiagnoses, leading to faster engine repairs and reduced downtime.
- Reduced Downtime: The ease of maintenance and efficient troubleshooting contribute to reduced downtime for the engine. By enabling quick and accurate repairs, the well-designed and documented wiring harness minimizes the time the engine is out of service, ensuring optimal engine availability and productivity.
In summary, the maintainability of a computer wiring harness for a DD15 engine is essential for reducing maintenance costs, minimizing downtime, and maximizing engine uptime. By prioritizing maintainability during the design and documentation stages, engineers can create a wiring harness that facilitates easy maintenance and troubleshooting, contributing to the overall efficiency and reliability of the engine.
A computer wiring harness for a DD15 engine is a crucial component that orchestrates the electrical communication and power distribution within the engine system. It serves as the backbone of the engine’s electrical infrastructure, ensuring seamless operation, reliability, and efficiency.
The wiring harness plays a vital role in transmitting signals between various sensors, actuators, and the engine control module (ECM). This intricate network of wires facilitates real-time data exchange, enabling the ECM to monitor engine parameters, make informed decisions, and optimize engine performance. Additionally, the wiring harness distributes electrical power to essential components, ensuring their proper functioning and contributing to the overall efficiency and reliability of the engine.
The design and construction of a computer wiring harness for a DD15 engine demand precision and adherence to industry standards. It requires careful planning, meticulous attention to detail, and the use of high-quality materials to withstand the harsh operating conditions of an engine. Proper installation and maintenance of the wiring harness are equally critical to ensure optimal engine performance and longevity.
FAQs on Computer Wiring Harness for DD15 Engine
Here are answers to some frequently asked questions about computer wiring harnesses for DD15 engines:
Question 1: What is the purpose of a computer wiring harness in a DD15 engine?
A computer wiring harness is an essential component of a DD15 engine that facilitates electrical communication and power distribution throughout the engine system. It connects various sensors, actuators, and the engine control module (ECM), enabling data exchange and optimizing engine performance.
Question 2: What are the key considerations in designing a wiring harness for a DD15 engine?
Designing a wiring harness for a DD15 engine involves meticulous planning, careful attention to detail, and adherence to industry standards. Engineers must consider factors such as the number and type of electrical components, the routing of wires, the operating environment, and the need for durability and reliability.
Question 3: What materials are commonly used in the construction of a wiring harness for a DD15 engine?
Wiring harnesses for DD15 engines typically use high-quality materials to withstand the harsh operating conditions. Common materials include copper or aluminum for wires, durable insulation to protect against heat and chemicals, and robust connectors to ensure secure connections.
Question 4: How can I ensure the proper installation and maintenance of a wiring harness in a DD15 engine?
Proper installation and maintenance of the wiring harness are crucial for optimal engine performance. Follow the manufacturer’s guidelines for installation, use high-quality tools, and regularly inspect the wiring harness for any damage or loose connections. Preventive maintenance measures, such as periodic cleaning and visual inspections, can extend the lifespan of the wiring harness and minimize the risk of electrical issues.
Question 5: What are the potential consequences of a faulty wiring harness in a DD15 engine?
A faulty wiring harness can lead to various issues, including engine control problems, reduced performance, increased emissions, and potential safety hazards. Electrical faults can disrupt signal transmission, power distribution, or both, affecting the proper functioning of engine components and compromising overall engine reliability.
Question 6: Where can I find additional information and resources on wiring harnesses for DD15 engines?
Refer to the engine manufacturer’s technical documentation, consult with authorized dealers or service centers, and explore reputable online resources for further information and support on computer wiring harnesses for DD15 engines.
By understanding these key aspects, you can gain a comprehensive overview of computer wiring harnesses for DD15 engines and their significance in ensuring optimal engine operation.
Transition to the next article section: Understanding the intricacies of computer wiring harnesses for DD15 engines empowers technicians, engineers, and end-users to make informed decisions, maintain high standards of engine performance, and ensure the longevity of their equipment.
Conclusion
In conclusion, the computer wiring harness plays an indispensable role in the performance, reliability, and efficiency of a DD15 engine. Its intricate network of wires and connectors orchestrates the flow of electrical signals and power, enabling seamless communication between various engine components. Understanding the significance of a well-designed and maintained wiring harness empowers technicians, engineers, and end-users to optimize engine operation and longevity.
As technology continues to advance, the complexity of engine wiring harnesses is likely to increase. By staying abreast of industry best practices, utilizing high-quality materials, and adhering to proper installation and maintenance procedures, we can ensure that these critical components continue to fulfill their essential role in the operation of DD15 engines and beyond.
Youtube Video:
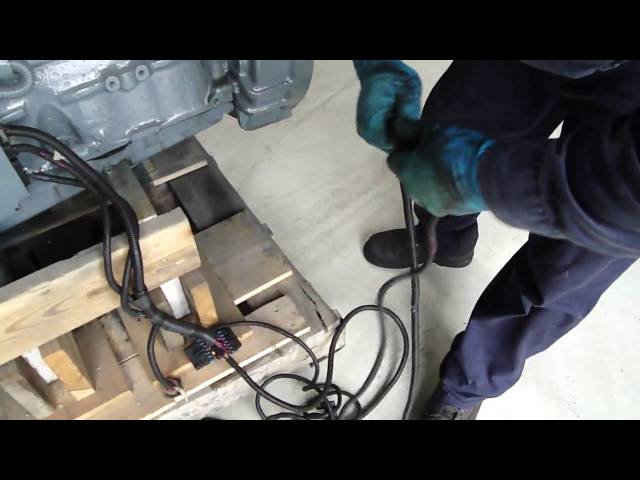