3 Phase Electric Motor Wiring Chart or Diagram
A 3 phase electric motor wiring chart or diagram is a visual representation of the electrical connections required to connect a 3 phase electric motor to a power source. It shows the different wires that need to be connected to the motor’s terminals, as well as the order in which they need to be connected.
There are many different types of 3 phase electric motor wiring charts and diagrams, but they all share some common features. Typically, they will include the following information:
- A diagram of the motor’s terminal block
- A list of the wires that need to be connected to each terminal
- The order in which the wires need to be connected
- Any special instructions that need to be followed
3 phase electric motor wiring charts and diagrams can be used for a variety of purposes, including:
- Troubleshooting motor problems
- Installing new motors
- Upgrading existing motors
- Designing new motor control systems
Using a 3 phase electric motor wiring chart or diagram can help to ensure that your motor is connected correctly and safely. It can also save you time and money by preventing costly mistakes.
Here are some tips for creating a 3 phase electric motor wiring chart or diagram:
- Start by identifying the motor’s terminal block. This is usually located on the back of the motor.
- Refer to the motor’s nameplate to determine the correct wiring configuration.
- Use different colored wires for each phase to avoid confusion.
- Make sure that all connections are tight and secure.
- Double-check your work before connecting the motor to a power source.
By following these tips, you can create a 3 phase electric motor wiring chart or diagram that is accurate, easy to understand, and safe to use.
Essential Aspects of 3 Phase Electric Motor Wiring
3 phase electric motor wiring is a critical aspect of motor operation and maintenance. Understanding the key aspects of 3 phase electric motor wiring is essential for ensuring safe and efficient operation.
- Power Source: 3 phase electric motors require a 3 phase power source to operate.
- Wiring Configuration: The wiring configuration of a 3 phase electric motor is determined by the motor’s design and the power source.
- Terminal Block: The terminal block is the point of connection for the motor’s power supply and control wires.
- Wire Size: The size of the wire used for 3 phase electric motor wiring is determined by the motor’s current draw.
- Conduit: Conduit is used to protect the wires from damage and to keep them organized.
- Grounding: Proper grounding is essential for the safe operation of a 3 phase electric motor.
- Overload Protection: Overload protection devices are used to protect the motor from damage in the event of an overload.
- Maintenance: Regular maintenance is essential to ensure the safe and efficient operation of a 3 phase electric motor.
These key aspects of 3 phase electric motor wiring are interconnected and essential for the safe and efficient operation of the motor. Proper wiring, grounding, and overload protection are critical for preventing accidents and damage to the motor. Regular maintenance is also essential to ensure that the motor continues to operate at peak efficiency.
Power Source
The connection between the power source and 3 phase electric motor wiring is fundamental to the operation of the motor. A 3 phase power source provides the necessary electrical energy to drive the motor, and the wiring configuration ensures that the power is delivered to the motor’s terminals in the correct sequence.
- Voltage and Current: The voltage and current supplied by the power source must match the requirements of the motor. If the voltage is too high, it can damage the motor’s windings. If the current is too high, it can cause the motor to overheat.
- Phase Sequence: The phase sequence of the power source must match the phase sequence of the motor’s windings. If the phase sequence is incorrect, the motor will not operate properly.
- Wiring Configuration: The wiring configuration of the motor must be compatible with the power source. There are different wiring configurations for different types of motors and power sources.
Proper 3 phase electric motor wiring is essential for the safe and efficient operation of the motor. By understanding the connection between the power source and the motor’s wiring, you can ensure that the motor is receiving the correct electrical power to operate properly.
Wiring Configuration
The wiring configuration of a 3 phase electric motor is a critical aspect of its operation. The wiring configuration determines how the motor’s windings are connected to the power source, and it affects the motor’s performance and efficiency.
- Motor Design: The motor’s design dictates the number of windings and the arrangement of the windings. This, in turn, determines the wiring configuration.
- Power Source: The power source also plays a role in determining the wiring configuration. The voltage and frequency of the power source must be compatible with the motor’s design.
There are different wiring configurations for different types of 3 phase electric motors. The most common wiring configurations are:
- Delta Connection: In a delta connection, the windings are connected in a triangle shape. This configuration is used for motors that are designed to operate at high speeds.
- Wye Connection: In a wye connection, the windings are connected in a Y shape. This configuration is used for motors that are designed to operate at low speeds.
The correct wiring configuration is essential for the safe and efficient operation of a 3 phase electric motor. Using the wrong wiring configuration can damage the motor or cause it to operate improperly.
Terminal Block
The terminal block is a critical component of 3 phase electric motor wiring. It is the point of connection for the motor’s power supply and control wires, and it plays a vital role in the safe and efficient operation of the motor.
The terminal block is typically located on the back of the motor, and it consists of a series of terminals that are connected to the motor’s windings. The power supply wires are connected to the line terminals, and the control wires are connected to the control terminals. The terminal block also provides a convenient point for connecting monitoring devices, such as ammeters and voltmeters.
Proper 3 phase electric motor wiring requires that the wires be connected to the correct terminals on the terminal block. If the wires are connected incorrectly, the motor may not operate properly, or it may even be damaged. It is important to consult the motor’s wiring diagram to ensure that the wires are connected correctly.
The terminal block is an essential component of 3 phase electric motor wiring. It provides a safe and convenient point for connecting the motor’s power supply and control wires, and it plays a vital role in the safe and efficient operation of the motor.
Wire Size
The size of the wire used for 3 phase electric motor wiring is a critical factor in ensuring the safe and efficient operation of the motor. The wire size must be large enough to carry the motor’s current draw without overheating. If the wire is too small, it will overheat and could cause a fire. Conversely, if the wire is too large, it will be more expensive and may not be necessary.
The motor’s current draw is determined by the motor’s power and efficiency. A more powerful motor will draw more current than a less powerful motor. Similarly, a less efficient motor will draw more current than a more efficient motor. The wire size must be selected based on the motor’s specific current draw.
There are a number of different ways to determine the correct wire size for a 3 phase electric motor. One common method is to use a wire size calculator. Wire size calculators are available online and in electrical engineering handbooks. Another method is to consult the motor’s manufacturer. The manufacturer will be able to provide the correct wire size for the specific motor.
Using the correct wire size is essential for the safe and efficient operation of a 3 phase electric motor. By understanding the connection between wire size and motor current draw, you can ensure that your motor is properly wired.
Conduit
In the context of 3 phase electric motor wiring, conduit plays a vital role in ensuring the safe and reliable operation of the motor. Conduit is a protective enclosure that houses and protects the electrical wires from external factors that could cause damage or disruption.
- Protection from Physical Damage: Conduit provides a physical barrier that shields the wires from mechanical damage, such as impacts, crushing, or abrasion. This is particularly important in industrial environments where heavy machinery and equipment are present.
- Protection from Environmental Factors: Conduit protects the wires from exposure to moisture, dust, and other environmental hazards. Moisture can cause corrosion and electrical shorts, while dust and debris can accumulate on the wires and interfere with their proper functioning.
- Organization and Routing: Conduit helps to organize and route the wires in a neat and efficient manner. It keeps the wires separated and prevents them from becoming tangled or crossing each other, which can lead to electrical problems.
- Improved Aesthetics: Conduit can improve the overall aesthetics of an electrical installation by concealing the wires and creating a more finished appearance.
Properly installed conduit is essential for the safe and reliable operation of 3 phase electric motors. By protecting the wires from damage and environmental factors, conduit helps to extend the life of the motor and prevent costly downtime.
Grounding
Grounding is an essential aspect of 3 phase electric motor wiring. It provides a low-resistance path for electrical current to flow to the ground in the event of a fault, protecting the motor, personnel, and equipment from electrical shock and damage.
Without proper grounding, a fault in the motor’s windings or insulation could cause the motor’s frame to become energized. This could create an electrical shock hazard for anyone who comes into contact with the motor, and it could also damage the motor itself and other connected equipment.
Proper grounding involves connecting the motor’s frame to a grounding electrode, which is typically a metal rod driven into the ground. The grounding electrode provides a low-resistance path for electrical current to flow to the ground, preventing it from flowing through the motor’s frame or other unintended paths.
There are a number of different methods for grounding a 3 phase electric motor. The most common method is to use a grounding lug that is connected to the motor’s frame. The grounding lug is then connected to the grounding electrode using a grounding wire.
Another method of grounding a 3 phase electric motor is to use a grounding bar. A grounding bar is a metal bar that is connected to the motor’s frame and to the grounding electrode. Grounding bars are often used in industrial settings where multiple motors are connected to a common grounding system.
Proper grounding is essential for the safe and reliable operation of a 3 phase electric motor. By providing a low-resistance path for electrical current to flow to the ground, grounding helps to protect personnel and equipment from electrical shock and damage.
Overload Protection
In the context of 3 phase electric motor wiring, overload protection is a critical aspect that ensures the motor’s longevity and safe operation. Overload protection devices are designed to safeguard the motor from potential damage caused by excessive electrical current, which can occur due to various factors such as mechanical overloads, voltage fluctuations, or short circuits.
- Protection against Electrical Faults: Overload protection devices, such as fuses or circuit breakers, act as a safety mechanism by interrupting the flow of excessive current in the event of an overload. This prevents the motor’s windings from overheating and potentially causing a burnout.
- Prevention of Mechanical Damage: Overloads can also result in mechanical damage to the motor, such as bearing failure or rotor seizure. Overload protection devices help prevent these issues by promptly disconnecting the motor from the power source, minimizing the risk of catastrophic damage.
- Enhanced Motor Reliability: By protecting the motor from overloads, overload protection devices contribute to its overall reliability and lifespan. A well-protected motor is less likely to experience premature failures, reducing downtime and maintenance costs.
- Compliance with Safety Regulations: Many industries and regions have specific regulations and codes that require the use of overload protection devices for electric motors. These regulations are in place to ensure the safety of personnel and equipment.
In summary, overload protection is an essential element of 3 phase electric motor wiring. By safeguarding the motor from excessive current, overload protection devices play a crucial role in preventing damage, enhancing reliability, and ensuring compliance with safety standards.
Maintenance
Regular maintenance is a crucial aspect of 3 phase electric motor wiring as it directly impacts the safety, performance, and longevity of the motor. By adhering to proper maintenance practices, potential issues can be identified and addressed promptly, minimizing the risk of costly repairs or unexpected downtime.
- Inspection and Cleaning: Regular inspections and cleaning of the motor and its components, such as terminals, connections, and windings, help maintain optimal performance. Dirt, dust, and debris can accumulate over time, potentially leading to insulation breakdown or electrical faults. Proactive cleaning and inspection mitigate these risks.
- Bearing Lubrication: Proper lubrication of the motor’s bearings is essential to reduce friction and prevent premature wear. Regular lubrication ensures smooth operation, extends bearing life, and minimizes noise and vibration.
- Electrical Testing: Periodic electrical testing, including insulation resistance tests and continuity checks, helps identify potential electrical faults or deterioration of components. Early detection allows for timely repairs, preventing catastrophic failures and ensuring the safety of personnel and equipment.
- Monitoring and Diagnostics: Advanced monitoring systems and diagnostic tools can provide valuable insights into the motor’s health and performance. By continuously monitoring parameters such as temperature, vibration, and current draw, potential issues can be identified at an early stage, enabling proactive maintenance and avoiding unexpected breakdowns.
Regular maintenance plays a vital role in extending the lifespan of a 3 phase electric motor, reducing the likelihood of costly repairs, and enhancing its overall efficiency and reliability. By incorporating comprehensive maintenance practices into the wiring and operation of 3 phase electric motors, businesses can ensure optimal performance, minimize downtime, and maintain a safe and productive work environment.
3 Phase Electric Motor Wiring: A Comprehensive Guide
3 phase electric motor wiring involves the electrical connections necessary to power and control a 3 phase electric motor. It ensures the efficient and safe operation of the motor, enabling it to convert electrical energy into mechanical energy for various industrial and commercial applications.
Proper wiring is crucial for optimizing motor performance, preventing electrical hazards, and extending its lifespan. Understanding the principles and best practices of 3 phase electric motor wiring is essential for electricians, technicians, and anyone involved in the installation, maintenance, or operation of electric motors.
This comprehensive guide will delve into the key aspects of 3 phase electric motor wiring, covering topics such as power source requirements, wiring configurations, terminal block connections, wire sizing, grounding, overload protection, and regular maintenance. By exploring these topics, readers will gain a thorough understanding of the intricacies of 3 phase electric motor wiring, empowering them to ensure the safe, efficient, and reliable operation of these essential electrical machines.
FAQs on 3 Phase Electric Motor Wiring
This section addresses frequently asked questions (FAQs) related to 3 phase electric motor wiring, providing concise and informative answers to common concerns or misconceptions.
Question 1: What are the key considerations for selecting the appropriate wire size for a 3 phase electric motor?
Answer: The wire size should be determined based on the motor’s current draw, which is influenced by its power and efficiency. Using a wire size calculator or consulting the motor manufacturer’s specifications helps ensure the selected wire can safely carry the required current without overheating.
Question 2: Why is proper grounding crucial for 3 phase electric motor wiring?
Answer: Proper grounding provides a low-resistance path for electrical current to flow to the ground in case of a fault, protecting personnel and equipment from electrical shock and damage. It also prevents the motor’s frame from becoming energized, minimizing the risk of electrical hazards.
Question 3: What is the purpose of overload protection devices in 3 phase electric motor wiring?
Answer: Overload protection devices, such as fuses or circuit breakers, safeguard the motor from damage caused by excessive electrical current. They interrupt the current flow in the event of an overload, preventing overheating and potential burnout of the motor’s windings.
Question 4: What are the essential steps involved in wiring a 3 phase electric motor to a power source?
Answer: The wiring process typically involves identifying the motor’s terminal block, determining the correct wiring configuration based on the power source and motor design, connecting the wires to the appropriate terminals, and ensuring secure and proper connections.
Question 5: How does regular maintenance contribute to the longevity and efficiency of a 3 phase electric motor?
Answer: Regular maintenance practices, such as inspections, cleaning, lubrication, electrical testing, and monitoring, help maintain optimal performance, extend the motor’s lifespan, and prevent unexpected breakdowns. By addressing potential issues early on, maintenance helps ensure the motor operates safely, efficiently, and reliably.
Question 6: What are the potential consequences of improper 3 phase electric motor wiring?
Answer: Improper wiring can lead to a range of issues, including motor damage, electrical hazards, reduced efficiency, and premature failure. It can also compromise the safety of personnel and equipment, highlighting the importance of adhering to proper wiring practices and seeking professional assistance when necessary.
These FAQs provide a foundation for understanding the critical aspects of 3 phase electric motor wiring. By addressing common concerns and misconceptions, they empower individuals to make informed decisions and ensure the safe and effective operation of these essential electrical machines.
For more comprehensive information, refer to the corresponding sections within this guide, where each topic is explored in greater depth.
Conclusion
Throughout this comprehensive guide, we have explored the intricacies of 3 phase electric motor wiring, emphasizing its critical role in the safe, efficient, and reliable operation of these essential electrical machines. Proper wiring practices are paramount to harness the full potential of 3 phase electric motors, ensuring they deliver optimal performance and longevity.
By understanding the principles and best practices outlined in this guide, individuals can make informed decisions regarding the wiring and maintenance of 3 phase electric motors. Proper selection of wire size, grounding, overload protection, and regular maintenance are key factors that contribute to the safety, efficiency, and longevity of these motors. Neglecting these aspects can lead to costly repairs, unexpected breakdowns, and potential hazards.
Investing in proper 3 phase electric motor wiring is not only a wise financial decision but also a crucial step towards ensuring a safe and productive work environment. By adhering to industry standards and best practices, individuals can harness the full potential of these powerful machines and contribute to the smooth operation of various industrial and commercial applications.
As technology continues to evolve, we can expect advancements in 3 phase electric motor wiring techniques and materials. However, the fundamental principles outlined in this guide will remain essential for the safe and effective operation of these motors. By embracing these principles and staying abreast of industry developments, individuals can ensure the continued success and efficiency of 3 phase electric motors in the years to come.
Youtube Video:
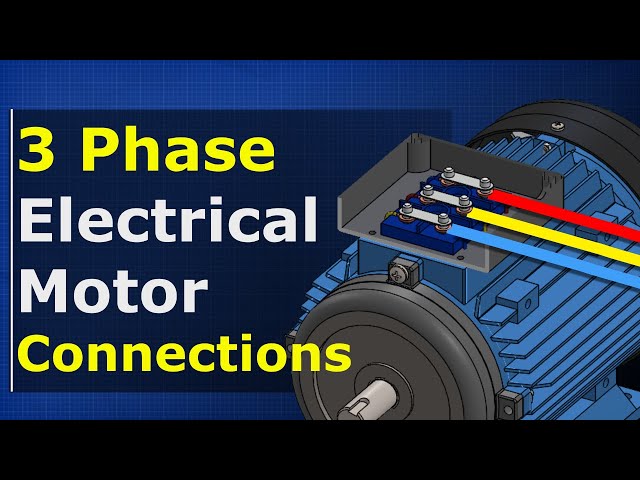